Laura Munteanu, Rompetrol Quality Control: ”We are, in one way, the physicians of the refinery”
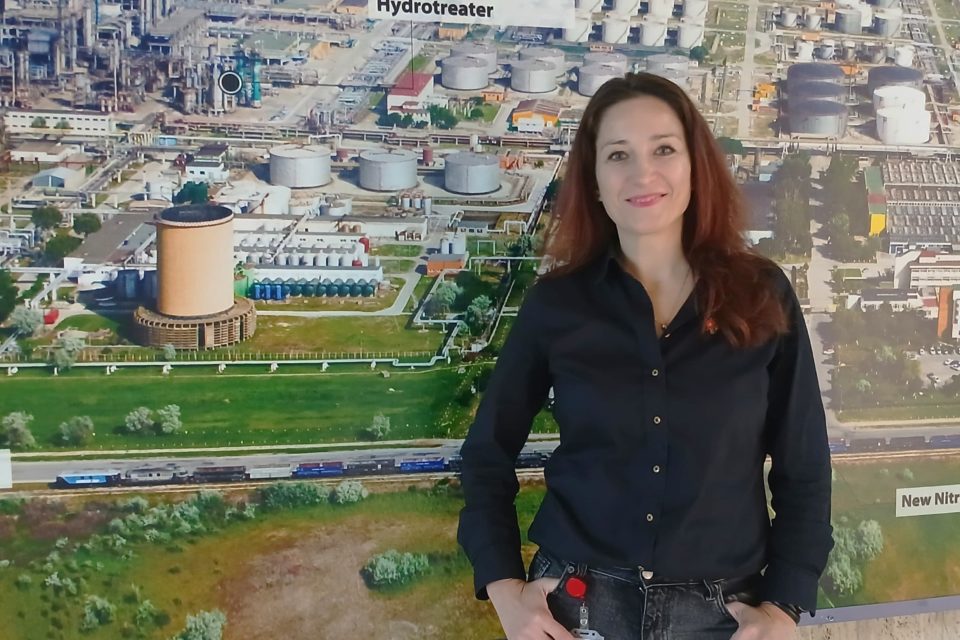
Journey into the refinery’s past and present
Over 45 years ago, Petromidia began writing its history on the seashore, in Năvodari. The decision to locate the refinery was made after a helicopter flyover, determining that the current location met all the essential conditions: proximity to the sea, a town that could be developed, and a vast amount of available space.
Continuous modernizations supported by the sole shareholder, KazMunayGas, such as the major investment project in the period 2008-2012, increased the refinery’s capacity to 5 million tons, consolidating its status as a national and regional leader.
Petromidia is a refinery with a high complexity index and processes high-sulfur crude oil, obtaining exclusively Euro 5 products. Petromidia works integrated with Vega, the second refinery of the Group, to which it sends semi-finished products that result in value-added products. Vega is the only local producer of road bitumen and polymer-modified bitumen.
Also within the Petromidia refinery, the only petrochemical unit in Romania operates. In 2008, the refinery put into operation the only marine terminal, located 8.6 km from the Midia Port, which supplies the refinery with crude oil through underground and land pipelines. In 2020, amid the COVID-19 pandemic, Petromidia developed a new petrochemical grade, used for the filter material in protective masks, thus marking a continuous adaptation of the refinery. After years of successive financial losses, caused by market volatility, 2022 was one of the best years in Rompetrol’s history. Petromidia is one of the main engines of industries in the region, with new production records.
The insights shared by specialists of Rompetrol Quality Control (RQC), the laboratory division of the KMG International group or the “doctor” of the Petromidia and Vega refineries:
When you are part of a company that offers services in a niche segment, you know that the standard of quality must be very high and that there is no room for mediocrity. This is also the case with the employees of Rompetrol Quality Control (RQC), the laboratory division of the KMG International group or the “doctor” of the Petromidia and Vega refineries, as Laura Munteanu, Commercial Manager at RQC, told us. As a landmark in the market of full service testing providers, RQC has managed to pass the time as a family where tasks are very clearly divided and where success is guaranteed thanks to highly trained people.
How long have you been employed by the company and what does the job entail?
I have been employed in Rompetrol Quality Control (RQC) since its establishment, in 2004, and in the KMG Rompetrol group, since 2002, right after I graduated from university. I am in charge of coordinating the sales activity, all in close connection with the other departments within the company, because together we have the same goal: the delivery of comprehensive and high-quality testing services in accordance with the requirements of our customers.
What made you want to work here?
I knew that I wanted to work in Petromidia, since I was in school, because I attended the courses of the “Ovidius” University in Constanța, majoring in Petroleum Processing Technology and Petrochemistry. For those who do not know what Rompetrol Quality Control does, we must say that we are the laboratory division of the KMG International group, which directly supports the activity of the Petromidia Năvodari and Vega Ploiesti refineries, but also the only petrochemical division in Romania. At the beginning of my career, the laboratories were integrated in the refinery and petrochemicals, and following the interview, I was selected for the position of petrochemical engineer, for the Petroleum Products Laboratory. There I developed from a professional point of view, and in 2004, with the establishment of RQC and the desire of the top management to develop the business outside the group, I started the beautiful journey in the field of sales. I’ve enjoyed this branch so much because I interact with people so much that any other challenges or temptations I’ve had along the way, I’ve come back here.
What does working in RQC mean for you and your career?
RQC means to me people close to my heart, good professionals, a team where I learned that there is no such thing as the phrase “I can’t do this!”. For us, quality and precision in the services we have in our portfolio are paramount, that’s why I promote them with all openness. This company also means the experience shared with our young colleagues, who are now my age since employment. RQC stands for all the beautiful projects we’ve been a part of. I dare say that the work in RQC is a challenge, but also a joy, every day. That’s because no day is the same.
What impact did the existence of such a laboratory have for the refinery, but also for the development of the area?
We are, in a certain way, the doctor of the refinery, because our indicators show if the refinery is healthy, that is, if the products it produces are of high-quality standards that we are used to offering and with which we have usual customers. We ensure quality control, as it is also found in the name of the company, so the importance of our laboratories, on both platforms (Petromidia and Vega) in the whole process is very high, starting with sampling, testing and then validating the results, thus guaranteeing the quality of Rompetrol brand products. RQC is a landmark on the market of full service providers of testing environmental factors (water, air, soil), waste (leachated/eluted), professional noxes, mask and breathing apparatus checks, petroleum products (liquid, solid, gaseous), biofuels, petrochemicals, environmentally friendly solvents, road bitumens, polymer-modified bitumens and bituminous binders.
How important is the team to work in a company like RQC?
We talk about the team everywhere, starting with the family, the school, then the company we work in, because most of us are made to function, shape and grow, alongside each other. And yes, in RQC the performance and the high level of quality are the result of the involvement of all 215 employees of the company. We know that we can only function together.
How has working with people helped you to evolve?
I like to observe people in all their states, I like the challenges of our emotions, which we should try to manage in positive ways, so that in the end the result is a success! Every day, in sales, you have many interactions with all kinds of characters, and if you don’t know how to listen to people, empathize with them, get to instill in them that you are the right business partner for them, you will not had good results.
Is there a lesson that you have learned in these years of activity that you would pass on?
“The Golden Rule for Every Business is this: Put Yourself in your Customer’s Place.” – Orison Swett Marden. This is the rule by which I have guided myself in my work and which I try to pass on to younger people.