Salzgitter AG, E.ON and Linde start operating an industrial hydrogen production plant based on electricity from wind power
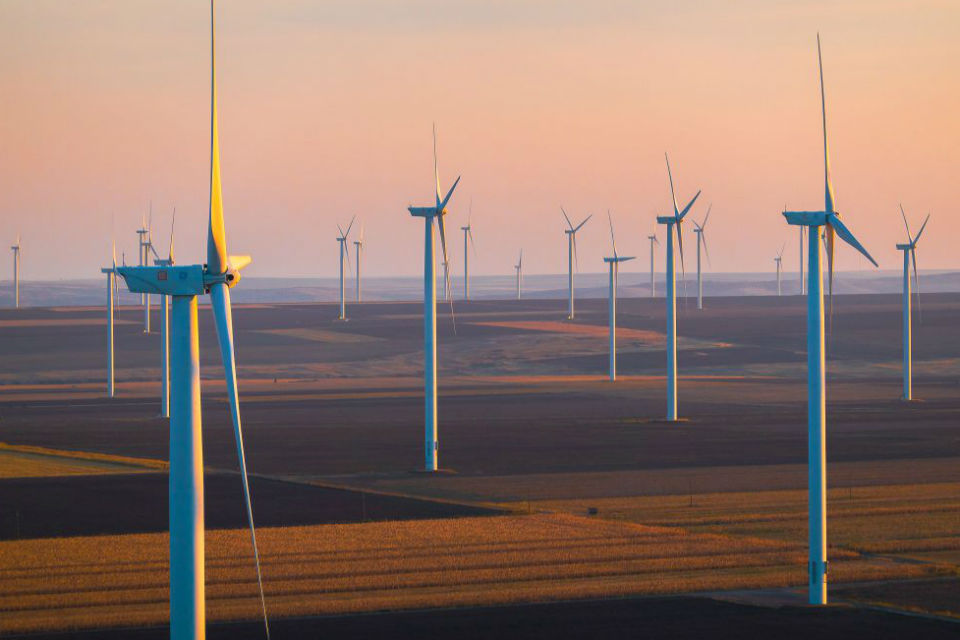
Salzgitter AG, E.ON subsidiary Avacon and Linde have taken an important and unprecedented step towards decarbonizing the steel industry. With the commissioning of the “Wind Hydrogen Salzgitter – WindH2” sector coupling project, the only one of its kind in Germany, green hydrogen will in future be produced on the site of the Salzgitter steelworks using electricity from wind energy.
WindH2 is a central component of the SALCOS® – Salzgitter Low CO2 Steelmaking technology project developed by Salzgitter AG. SALCOS describes the most efficient and timely way to reduce CO2 emissions, and in the long term even to achieve almost CO2-free steel production. Hydrogen generated from renewable sources will replace the carbon previously required for iron ore smelting. The three blast furnaces currently in operation will have to be gradually replaced by a combination of direct reduction plants and electric arc furnaces. Such a transformation of steel production could reduce CO2 emissions by around 95 percent by 2050.
The newly constructed facilities were presented to the public today in Salzgitter. Among those present at the opening were State Secretary Andreas Feicht, Federal Ministry for Economic Affairs and Energy; Dr. Bernd Althusmann, Lower Saxony Minister for Economic Affairs, Labor, Transport and Digital Affairs; Olaf Lies, Lower Saxony Minister for the Environment, Energy, Building and Climate Protection; Dr. Johannes Teyssen, CEO of E.ON SE; Marten Bunnemann, CEO of Avacon AG, and Prof. Dr.-Ing. Heinz Jörg Fuhrmann, CEO of Salzgitter AG.
Avacon operates seven newly constructed wind turbines with a total capacity of 30 megawatts on the Salzgitter AG site. Salzgitter Flachstahl GmbH has installed two Siemens 1.25 megawatt PEM electrolysis units centrally on the plant site, which will generate around 450 cubic meters of high-purity hydrogen per hour. Hydrogen is already used in steel production for annealing processes and in the hot-dip galvanizing lines. Industrial gas producer Linde currently supplies the gas by truck and will continue to ensure a continuous supply of hydrogen in the future. All the plants are currently in trial operation. With “WindH2”, the partners want to gain know-how and experience with the on-site production of wind power and hydrogen, as well as their integration into the complex procedures and processes of an integrated steelworks. The costs for the entire project amount to around 50 million euros. The construction of the electrolysis plant was funded by KfW.